
Sample applications
Mechanical engineering
Consistently keeping wear to a minimum has a crucial influence on stability, service life and cost-effectiveness in mechanical engineering.
In this context, KVT Kurlbaum AG serves as your professional development and strategic partner.
Sample applications
Industries:
Mechanical engineering, drilling, pump construction
Context:
- Wear-resistance to prevent cavitation erosion
- The protective sleeve helps to regulate flow volumes
- Sediments and strong medium flows expose the inner diameter to cavitation erosion
- A sufficiently thick wear-resistant coating is needed
KVT solution:
Coating method: HVOF
Coating material: KVT 176®
Base material: 1.4571
Benefits to the customer:
High-velocity oxygen fuel spraying (HVOF) applies little thermal energy but a lot of kinetic energy. As such, it strikes the right balance between adhesive strength for the coating and minimal stress for the base material. It is also technically feasible to coat the inside of components using this method. Low thermal input means that there is no impact on the base material.
We use a tungsten carbide such as KVT 176® as the coating material. Based on tungsten carbide, cobalt and chromium, this coating provides optimal wear-resistance for this application. It also permits thin coatings of 0.3 mm to a tolerance of ±0.1 mm. Narrow tolerances can thus be observed for the entire installation.
Industries:
Mechanical engineering, pump construction
Context:
The plunger operates in a cylinder that is filled with hot particle-reinforced plastic in liquid form. The piston pumps a prescribed volume of plastic into the system for bonding. The particle-reinforced adhesive, the temperature and the narrow gap to the cylinder walls combine to cause significant abrasive wear that is further amplified by the large number of piston strokes.
Roughness values of Rz ≤ 0.1(0.05–0.08) can be realized.
KVT solution:
Coating method: HVOF
Coating material: KVT 251®
Base material: 1.4571 or 1.4301
Benefits to the customer:
High-velocity oxygen fuel spraying (HVOF) applies little thermal energy but a lot of kinetic energy. As such, it strikes the right balance between adhesive strength for the coating and minimal stress for the base material. It can also be applied to all common materials.
We use KVT 251 as the coating material. KVT 251 is a chromium carbide that is reinforced with tungsten carbide to enable coating thicknesses of 0.1-0.2 mm to resist temperatures of up to 550 °C and achieve hardness levels of up to 1,200 HV/0.3.
The coating method and coating material selected enable a very resilient, thin, wear-resistant coating to be applied to any base material. The coating can then be ground to achieve the prescribed roughness value.
Combined factors:
Wear-resistance and scuffing reduction
Industries:
Mechanical engineering, high-pressure pump construction
Context:
The plunger operates in a guide sleeve. To avoid scuffing of both the plunger and the guide sleeve, the plunger is given a bonded coating on top of the KVT 251® coating.
The bonded coating effectively provides permanent lubrication for sliding parts and in the case of high wear. It boasts good antifriction properties with low friction coefficients and substantial pressure absorption capacity.
KVT solution:
Coating method: HVOF and bonded coating
Coating material: KVT 251® and bonded coating
Base material: 1.4571 or 1.4301
Benefits to the customer:
High-velocity oxygen fuel spraying (HVOF) applies little thermal energy but a lot of kinetic energy. As such, it strikes the right balance between adhesive strength for the coating and minimal stress for the base material. It can also be applied to all common materials. Application of the bonded coating likewise involves little thermal energy and subjects the component to no additional stress.
Applying KVT 251® and bonded coatings creates powerful wear-resistance and reduces the friction coefficient. This translates into a significantly longer service life for the coated product.
Combined factors:
Corrosion- and wear-resistance
Industries:
Mechanical engineering, packaging industry
Context:
Forging rolls are used to carry, transport and process PET strips (highly abrasive packaging material). The rolls/godets can also be heated from the inside. On the outer running surface, components must be protected from wear. In addition, internal heating leads to condensation, which can have a corrosive effect.
KVT solution:
Coating method: Chemical nickel plating and HVOF
Coating material: Chemical nickel and KVT 175®
Base material: Unalloyed steel
Benefits to the customer:
Applying a 50-µm layer of nickel plating gives the substrate a non-porous coating that protects it from corrosion. High-velocity oxygen fuel spraying (HVOF) is then used to coat the nickel-plated surface with a 0.1-0.3 mm layer of tungsten carbide JVT 175®. Finally, the surface can also be ground to achieve defined roughness values.
This combination of nickel phosphate and tungsten carbide coatings can substantially extend a component's service life.
Context:
Valves made of Inconel are needed for the chemical industry.
Given a nominal size of DN 200, however, it would be extremely expensive to make the entire valve body from Inconel.
The medium contains natural sediments that have an abrasive effect when subject to high flow velocities. It also contains aggressive chemical components that would even react with normal stainless steels.
The assemblies are safety-critical and must never be allowed to fail in their entirety.
KVT solution:
Coating method: Laser, spray-and-fuse process
Coating material: KVT 404®/KVT 433®
Base material: 1.4462
All internal parts of the valve that come into contact with the medium are cladded using the laser-welding method. The points at which seals and washers are affixed are turned to create a perfect fit to tolerances of within a few hundredths of a millimeter.
Balls and washers are flame-sprayed and fused with a combination of KVT 404 and KVT 433. The components are lapped against each other in pairs for an impermeable fit.
Benefits to the customer:
Cladding the valve with Inconel avoids the expense of using solid materials and reduces production costs for the valve body by more than 50 percent. The material is subject only to superficial thermal stresses and retains its full mechanical performance capabilities.
The laser-welding method creates a permanent metallurgical bond between the substrate and the protective Inconel cladding. This eliminates the threat of sub-surface corrosion and the resultant risk that the cladding might flake off.
Over more than three decades, the combination of KVT 404 and KVT 433 hard alloy coatings has proven itself in thousands of installations involving all kinds of media. It also delivers the longest known service lives in the industry. Thanks to a high nickel content, these coatings are very well protected against chemical corrosion. The spray-and-fuse process produces virtually non-porous coatings, and the metallurgical bond almost completely precludes the possibility of sub-surface migration.
Why KVT?
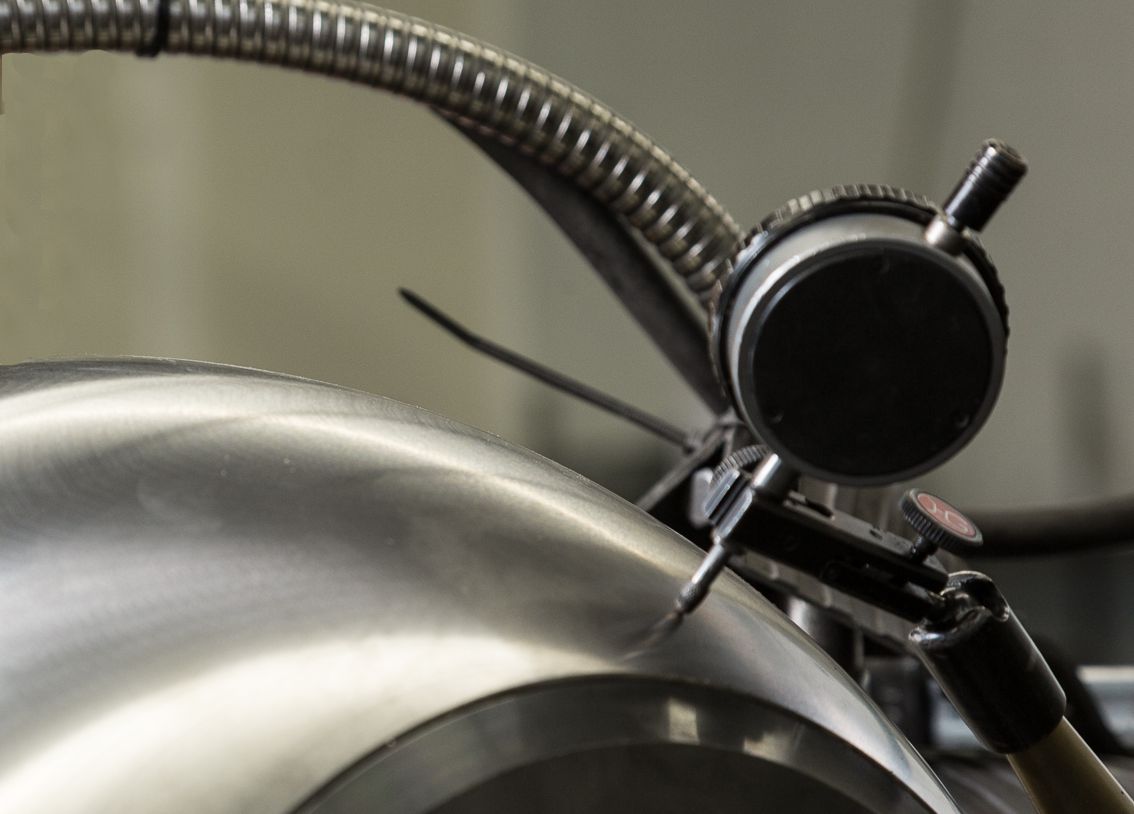
What sets us apart
Whenever abrasion, high temperatures, high pressure levels, large numbers of cycles and high flow velocities are critical factors, we are the people to talk to.
More detailsDownloads
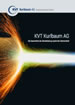
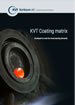